Corrosion monitoring is the process of evaluating and monitoring signs of corrosion in equipment components, structures, process units, and equipment. Monitoring programs are designed to identify specific conditions to extend asset life and serviceability while increasing safety and reducing replacement costs. Corrosion monitoring includes all types of corrosion and materials.
A major benefit of installing a corrosion monitor is the early identification of warning signs of corrosion and the ability to identify trends and process parameters that may create a corrosive environment. Processing parameters that may need to be changed include temperature, pressure, pH, etc. Additionally, corrosion monitoring is used to measure the effectiveness of corrosion control methods to determine if other inspection and/or monitoring techniques should be employed.
How is corrosion monitored
Corrosion monitoring includes a wide range of techniques for measuring, controlling and containing corrosion. These methods can be broadly classified into two types: “inspection” and “monitoring.”
Inspection technology
Before employing any inspection technique, it is important to document the operating parameters of the equipment. This increases the chance of corrosion occurring. These parameters include system pH, flow rate (velocity), pressure and temperature. Nondestructive testing (NDT) and inspection techniques are then performed to identify the nature of corrosion damage. Common NDT methods for detecting corrosion include ultrasonic inspection, X-ray inspection, magnetic flux leakage, etc.
Risk-based inspection and conformity assessment are additional methods and processes that can complement your oversight program. These methods include qualitative and quantitative approaches and provide information about the current state of the equipment and information about the remaining life of the equipment.
Monitoring Techniques
Once corrosion has been identified, corrosion measurement techniques can be used to gather information about the corrosive environment. This is accomplished through the use of probes, which are mechanical, electrical, or electrochemical devices that monitor corrosive changes during operation. In addition, corrosion measurement techniques can be used to provide direct and indirect information about processes, either online (i.e. in-service) or off-process. Common corrosion measurements include pH measurements and microbiological analyses. Analytical chemistry techniques provide information on the amount of dissolved gases (O2, CO2, H2S, etc.) and the oxidation of metal ions (Fe2, Fe3, etc.).
Corrosion monitoring technology allows direct measurements while the process unit is in operation. Common monitoring techniques include the use of corrosion probes, electrical resistance, linear polarization resistance, and galvanic monitoring. Advanced monitoring techniques include biological monitoring, ultrasonic thickness monitoring, and hydrogen permeation monitoring.
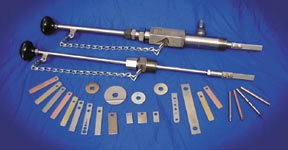
Corrosion coupon (or mass loss coupon) testing is the simplest form of corrosion monitoring applicable to any environment (gas, liquid, slurry, etc.). A coupon is a sample that matches the material of the monitored device. Coupons are placed in a process environment and removed after a period of time (eg, weeks or months). Next, 1) the amount of mass loss, 2) the type of corrosion, and 3) the corrosion rate are analyzed.
Electrical resistance probes measure the change in electrical resistance of a component and provide information on metal loss. These probes can be used for a long time in any environment. In addition, it can provide periodic (e.g. daily, weekly, monthly) or continuous (e.g. hourly) data on corrosion rates.
Linear polarization resistance is an electrochemical technique in which a current is passed through the electrodes and the corrosion rate is measured instantly. The main drawback of these techniques is that they can only be performed in conductive media and aqueous solutions.
Galvanic monitoring, also called zero resistance current measurement, is another electrochemical technique that measures the galvanic current flowing between two different electrodes. The results give information about the oxygen content in the medium.
Biological monitoring measures the presence of bacteria that consume sulfate and produce sulfuric acid (H2SO4). Sulfuric acid is known to be highly corrosive to metal equipment. Ultrasonic thickness monitoring is a widely used NDT method for measuring the wall thickness of components over time. This technology is very sensitive and can scan large areas with ultrasound.
Hydrogen penetration monitoring uses a probe to measure the amount of hydrogen dissolved in steel parts. In the oil and gas industry, hydrogen is often a by-product of many reactions and can lead to hydrogen cracking and hydrogen embrittlement if left untreated.
Overall, Corrosion surveillance technology has proven successful in reducing asset downtime, extending asset life and saving companies significant costs. Using multiple techniques simultaneously is not uncommon.
When is corrosion monitoring performed?
Corrosion monitoring plays an important role throughout the equipment lifecycle. Testing and monitoring strategies and techniques are subject to change depending on equipment age and condition. Therefore, inspection and monitoring strategies should be reviewed regularly at the discretion of owners and operators.
Where does corrosion monitoring take place? Corrosion remains one of the biggest threats to the oil industry. Corrosion protection is therefore of paramount concern, especially in equipment such as flow lines, transfer lines, vessels, water systems, boilers, vacuum towers, refrigeration systems, amine systems and crude oil systems. These systems tend to create the most corrosive environments.